The Challenge
One of the leading supplier of fully integrated drivetrain and electrified propulsion systems for all passenger vehicles, faces the challenge of:
- respecting an increasingly stringent specific product quality criteria;
- understanding the causes of increased waste levels;
- achieving problem anticipation in a perspective of Predictive Quality;
- timely preparation of a quick resolution.
The Solution
The focus is the production of the synchronizer ring in the plant in South of Italy, specialized in the mechanical components for the automotive market.
The Machine Learning methodology, in particular the classification algorithms, identifies the generative factors of waste elements in the manufacturing chain, monitoring specific features.
Following pre-defined steps, such as Feature Selection, Pearson’s Correlation, Classification and Model Training, the implemented algorithm learns how to classify the observations starting from a set previously labelled of time window historical data and not analysed a predefined output.
The collected data is also used to compile a near real-time Business Intelligence dashboard containing some useful process performance indicators.
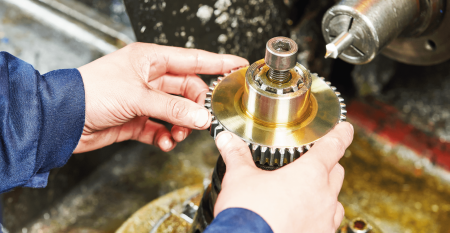
The Benefits
For each specific use case the most suitable ML algorithm reaches the final objective evaluating KPIs such as: Precision, Recall, F-Measure, Accuracy.
Predictive Quality within the production process reduces presumed waste which results in both the recovery of the pieces produced and in greater higher revenues.